Laut der International Food Industry Federation (IFIF) wird die jährliche globale Produktion von zusammengesetzten Lebensmitteln auf mehr als eine Milliarde Tonnen geschätzt und der jährliche globale Umsatz der kommerziellen Lebensmittelproduktion auf mehr als 400 Milliarden US -Dollar (394 Milliarden Euro) geschätzt.
Futterhersteller können sich keine ungeplante Ausfallzeit oder verlorene Produktivität leisten, um mit der wachsenden Nachfrage Schritt zu halten. Auf Anlagenebene bedeutet dies, dass sowohl Geräte als auch Prozesse stabil sein müssen, um die Nachfrage zu befriedigen und gleichzeitig ein gesundes Endergebnis zu erhalten.
Die einfache Automatisierung ist wichtig
Das Fachwissen nimmt langsam ab, wenn ältere und erfahrene Arbeitnehmer in den Ruhestand treten und nicht mit der erforderlichen Rate ersetzt werden. Infolgedessen sind qualifizierte Futtermittelmaschinenarbeiter von unschätzbarem Wert und es besteht ein wachsender Bedarf, Prozesse auf intuitive und einfache Weise zu automatisieren, von den Betreibern bis hin zu Handhabungs- und Produktionsmanagement. Ein dezentraler Ansatz zur Automatisierung kann es beispielsweise schwierig machen, mit verschiedenen Systemen aus verschiedenen Anbietern zusammenzufassen, was an sich unnötige Herausforderungen erzeugen kann, was zu ungeplanten Ausfallzeiten führt. Probleme im Zusammenhang mit Ersatzteilen (Pelletmühle, Ring -Sterbchen, Futtermühle), die Verfügbarkeits- und Servicefunktionen auch zu kostspieligen Ausfallzeiten führen.
Dies kann leicht durch eine Partnerschaft mit einem Enterprise Solution -Anbieter vermieden werden. Denn das Unternehmen befasst sich mit einer einzigen Fachkompetenzquelle in allen Aspekten der Anlage und ihren damit verbundenen Prozessen sowie den relevanten regulatorischen Anforderungen. In einer Tierfutteranlage können Faktoren wie eine präzise Dosierung mehrerer Additive, die Temperaturkontrolle, die Kontrolle der Produktkonservierung und die Verringerung der Abfälle durch Waschen genau kontrolliert werden und gleichzeitig das höchste Niveau der Futtermittelsicherheit aufrechterhalten werden. Die Sicherheitsanforderungen für Futtermittel können erreicht werden. Nährwert. Dies optimiert den Gesamtbetrieb und letztendlich die Kosten pro Tonne Produkt. Um die Kapitalrendite zu maximieren und die Gesamtbesitzkosten zu senken, muss jeder Schritt auf den individuellen Betrieb zugeschnitten sein und gleichzeitig die volle Transparenz des Prozesses sicherstellen.
Darüber hinaus stellt die enge Kommunikation mit dedizierten Kontomanagern, mechanischen und Prozessingenieuren sicher, dass die technischen Fähigkeiten und Funktionen Ihrer Automatisierungslösungen immer geschützt sind. Diese Fähigkeit, den Prozess vollständig zu steuern, sorgt für das Produkt von höchster Qualität und fügt bei Bedarf den vorgelagerten und nachgelagerten Elementen integrierte Rückverfolgbarkeit hinzu. Alle Produktionsprozesse werden online oder vor Ort unterstützt, von der Bestellung des Steuerungssystems bis zur direkten Unterstützung über das Internet.
Maximierung der Verfügbarkeit: ein zentrales Problem
Fabriklösungen können als alles, was ein Teil bearbeitender Geräte bis hin zu Wand- oder Greenfield -Installationen, eingestuft werden. Der Fokus ist jedoch unabhängig von der Projektgröße gleich. Das heißt, wie ein System, eine Linie oder eine ganze Pflanze die erforderlichen positiven Auswirkungen liefert. Die Antwort liegt in der Art und Weise, wie Lösungen entworfen, implementiert und optimiert werden, um die maximale Verfügbarkeit gemäß den festgelegten Parametern bereitzustellen. Die Produktivität ist ein Gleichgewicht zwischen Investition und Rentabilität, und der Geschäftsfall ist die Grundlage für die Bestimmung, welches Niveau erreicht werden soll. Jedes Detail, das sich auf das Produktivitätsniveau auswirkt, ist ein Risiko für Ihr Unternehmen, und wir empfehlen dringend, den Experten den Experten zu überlassen.
Durch die Beseitigung der erforderlichen Verbindung zwischen Lieferanten mit einem einzelnen Anbieter von Enterprise Solutions haben Enterprise -Eigentümer einen Partner, der sowohl verantwortlich als auch rechenschaftspflichtig ist. Zum Beispiel erfordern Fabriken die Verfügbarkeit von Ersatzteilen und Verschleißteile wie Hammermill -Hämmer, Bildschirme, Rollenmühlen-/Flakemühlebrötchen, Pelletmühle, Mühlenrollen und Mühlenteile usw. Sie müssen in kürzester Zeit erhalten und von Fachleuten installiert und gepflegt werden. Wenn Sie ein Anbieter von Fabriklösungen sind, kann der gesamte Prozess ausgelagert werden, auch wenn einige Elemente einen Anbieter von Drittanbietern erfordern.
Wenden Sie dieses Wissen dann auf wichtige Bereiche wie die Prognose an. Zu wissen, wann Ihr System Wartung benötigt, ist entscheidend, um Ausfallzeiten zu verringern und die Produktivität zu steigern. Zum Beispiel arbeiten die Pelletmühle normalerweise rund um die Uhr. Dies ist daher für ihren erfolgreichen Betrieb von grundlegender Bedeutung. Die auf dem heutigen Markt verfügbaren Lösungen überwachen und optimieren die Leistung in Echtzeit, leiten Faktoren wie Vibration und warnen die Betreiber in Zeiten potenzieller Fehlfunktionen, damit sie Ausfallzeiten entsprechend planen können. In einer idealen Welt würden Ausfallzeiten in die Geschichtsbücher eingehen, aber in Wirklichkeit ist es. Die Frage ist, was passiert, wenn das passiert. Wenn die Antwort nicht "unser Fabriklösungspartner hat dieses Problem bereits gelöst", ist es vielleicht Zeit für eine Änderung.
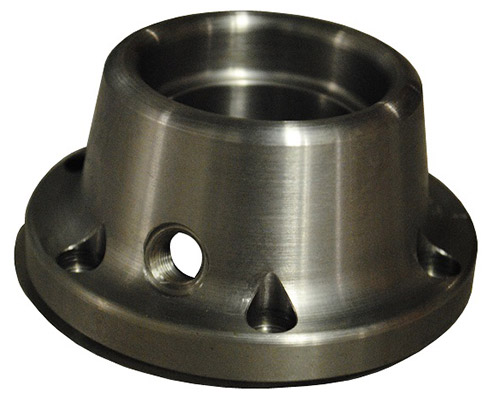
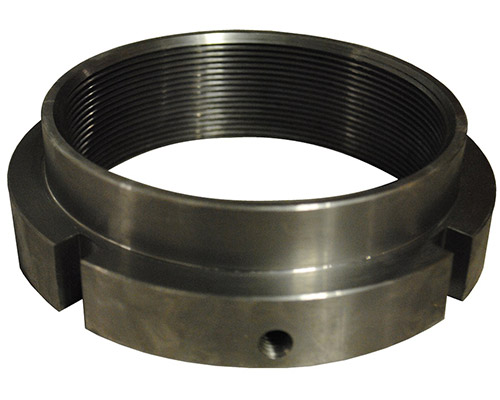