Según la Federación Internacional de la Industria Alimentaria (IFIF), la producción global anual de alimentos compuestos se estima en más de mil millones de toneladas y la facturación global anual de la producción de alimentos comerciales se estima en más de $ 400 mil millones (€ 394 mil millones).
Los fabricantes de alimentos no pueden permitirse el tiempo de inactividad no planificado o perder la productividad para mantenerse al día con la creciente demanda. A nivel de la planta, esto significa que tanto el equipo como los procesos deben ser estables para satisfacer la demanda mientras se mantiene un resultado final saludable.
La facilidad de la automatización es importante
La experiencia está disminuyendo lentamente a medida que los trabajadores mayores y experimentados se jubilan y no se reemplazan a la tasa requerida. Como resultado, los trabajadores de máquinas de alimentación calificada son invaluables y existe una creciente necesidad de automatizar los procesos de una manera intuitiva y fácil, desde los operadores hasta la gestión de la producción y el manejo. Por ejemplo, un enfoque descentralizado para la automatización puede dificultar la interactuación con diferentes sistemas de diferentes proveedores, lo que en sí mismo puede crear desafíos innecesarios, lo que resulta en un tiempo de inactividad no planificado. Sin embargo, los problemas relacionados con las piezas de repuesto (molino de pellets, matriz de anillo, molino de alimentación) y capacidades de servicio también pueden conducir a un tiempo de inactividad costoso.
Esto se puede evitar fácilmente asociándose con un proveedor de soluciones empresariales. Debido a que el negocio trata con una sola fuente de experiencia en todos los aspectos de la planta y sus procesos relacionados, así como los requisitos regulatorios relevantes. En una planta de alimentación animal, los factores como la dosificación precisa de varios aditivos, el control de la temperatura, el control de la preservación del producto y la reducción de desechos a través del lavado pueden controlarse con precisión, mientras se mantiene el nivel más alto de seguridad de los alimentos. Se pueden lograr los requisitos de seguridad de alimentación. Valor nutricional. Esto optimiza la operación general y, en última instancia, el costo por tonelada de producto. Para maximizar el retorno de la inversión y reducir el costo total de propiedad, cada paso debe adaptarse a la operación individual al tiempo que garantiza la transparencia total del proceso.
Además, la comunicación cercana con los gerentes de cuentas dedicados, los ingenieros mecánicos y de procesos asegura que la capacidad técnica y la funcionalidad de sus soluciones de automatización siempre estén protegidos. Esta capacidad de controlar completamente el proceso garantiza el producto de la más alta calidad y agrega trazabilidad incorporada a los elementos aguas arriba y aguas abajo cuando sea necesario. Todos los procesos de producción son compatibles en línea o en el sitio, desde ordenar el sistema de control hasta el soporte directo a través de Internet.
Maximización de disponibilidad: una preocupación central
Las soluciones de fábrica se pueden clasificar como cualquier cosa, desde equipos de mecanizado de piezas únicas hasta instalaciones de pared o campo verde, pero el enfoque es el mismo independientemente del tamaño del proyecto. Es decir, cómo un sistema, una línea o una planta completa proporciona lo que se necesita para producir efectos positivos. La respuesta radica en cómo se diseñan, implementan y optimizan las soluciones para proporcionar la máxima disponibilidad de acuerdo con los parámetros establecidos. La productividad es un equilibrio entre la inversión y la rentabilidad, y el caso comercial es la base para determinar qué nivel debe alcanzarse. Cada detalle que afecta los niveles de productividad es un riesgo para su negocio, y recomendamos que dejar la Ley de Balancing a los expertos.
Al eliminar la conexión necesaria entre los proveedores con un solo proveedor de soluciones empresariales, los propietarios de empresas tienen un socio que es responsable y responsable. Por ejemplo, las fábricas requieren disponibilidad de piezas de repuesto y piezas de desgaste como martillos Hammermill, pantallas, rollos de molino de molinos/escamas, troqueles de molinos de pellets, rollos de molino y piezas de molino, etc. Deben obtenerse en el tiempo más corto posible e instalados y mantenidos por profesionales. Si es un proveedor de soluciones de fábrica, incluso si algunos elementos requieren un proveedor de terceros, todo el proceso puede ser subcontratado.
Luego aplique este conocimiento a áreas importantes como el pronóstico. Saber cuándo su sistema necesita mantenimiento es fundamental para reducir el tiempo de inactividad y aumentar la productividad. Por ejemplo, Pellet Mill generalmente funciona las 24 horas del día, los 7 días de la semana, por lo que esto es fundamental para su operación exitosa. Las soluciones disponibles en el mercado hoy en día monitorean y optimizan el rendimiento en tiempo real, factores de guía como la vibración y los operadores advertidos en el tiempo de posibles mal funcionamiento para que puedan programar el tiempo de inactividad en consecuencia. En un mundo ideal, el tiempo de inactividad iría en los libros de historia, pero en realidad lo es. La pregunta es qué sucede cuando eso sucede. Si la respuesta no es "nuestro socio de solución de fábrica ya ha resuelto este problema", tal vez sea hora de un cambio.
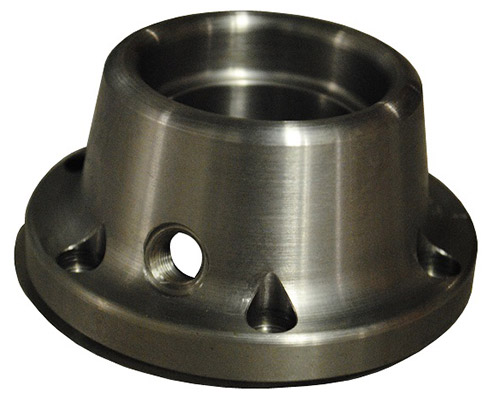
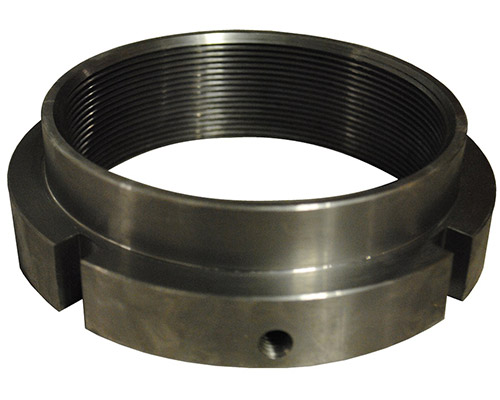